Canada has historically been at the forefront of science and technology. Its record of inventions is both enviable and diverse, including such items as Pablum, instant mashed potatoes, ginger ale, insulin, sonar, the walkie-talkie, the G suit and even Plexiglas.
One of the driving forces behind today’s innovations is Omachron Science, a research and development group right here in Hampton that has been together for 40 years, small in number but large in creativity, imagination and output. Omachron carries out significant research in energy-efficient small appliances, water and wastewater treatment including desalination, sustainable agriculture, low-cost solar power, improved HVAC systems, advanced LED lighting, energy-storage alternatives to batteries, and low-cost manufacturing and recycling for plastics, metals, glass and ceramics. It lives by its catchphrase: “Sustainable Technologies for a Better Future,”™ recognizing the obligation to allow current and future generations to live better.
The Omachron team, led by Wayne Conrad, has over 500 pending and granted patents. Omachron has licensed technology to many companies including Teledyne, Owens Corning, Climetec and SharkNinja. If you use a Shark product to clean your home, chances are you are using technology developed and patented by Omachron.
We have all seen the world become a global economy, and we have seen large companies become dominant in manufacturing as the required equipment and tooling have become increasingly expensive. Small entrepreneurs have had more than their share of challenges, but are now able to take advantage, on an unprecedented scale, of affordable 3D printers and CNC machines to prototype new ideas. However, mass production using 3D printing or CNC machines is not economically or technologically viable.
For over a decade now, the technical team at Omachron has focused on evolving technology that could empower and enable individuals and small companies, as well as larger companies, to take their ideas into production using 50% to 90% less capital, space, energy, and maintenance resources when compared to conventional manufacturing processes. Omachron has focused its efforts on five main areas: advanced floor care technology including vacuum cleaners; sustainable manufacturing and recycling for plastics, metals, glass and ceramics; ultra low energy LED lighting; energy efficient HVAC including low cost solar and biomass options; sustainable agriculture.
The recycling, molding and extrusion of plastics is one of the first of these projects that is now becoming a commercial reality. Omachron’s extrusion and molding processes use equipment 95% smaller than traditional equipment, and use 80% to 90% less energy to produce plastic parts. An Omachron injection molding machine, the size of an office desk, can replace a current machine which is the size of a railway locomotive. Moreover, it only uses about as much power as your home clothes dryer. An entrepreneur can start and run a molding or plastics extrusion business from their 2-car garage! The new molding process can be used to reproduce accurately micro-structures from smaller than a human hair to parts weighing hundreds of pounds. Importantly, the parts have little or no internal stress, meaning they will not deform over time after they are made.
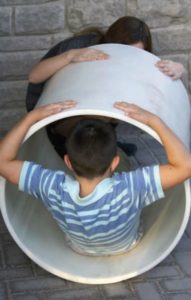
The new tooling methods developed at Omachron allow quick turnaround of tooling at a fraction of the cost of conventional extrusion or injection-molding tools. These technical features will enable small business to invest in projects in which conventional injection molding is not viable because the parts needed per year are too small, or because the parts wanted are too big. Figure 1 shows a mid-sized part made on a machine about the size of an office desk. The part is so big kids can play inside it! These breakthroughs in scale of equipment, energy usage and cost will enable distributed manufacturing throughout the world. Local production can be made for local consumption.
Omachron Looking Towards Future
Some of the first product offerings from Omachron that utilize this new technology are plastic sheets, rods and blocks. These items can be used in manual and CNC machines by hobbyists, makers, designers, model builders, furniture manufacturers, cabinet makers, prototyping bureaus and companies to make new products or prototypes. In the current marketplace, plastic blocks and rods for machining are only available in a limited range of sizes, colours and materials and custom plastic blends to improve material properties are very difficult and expensive to obtain.
Starting in November 2018, Omachron expects to open its custom services lab to the public to provide its PLASTI-BLOCK™ line of blocks, rods and custom shapes with proprietary colour blending and specialized additives in batches as small as 150 lbs., with lead times in as little as 5 to 10 business days. Omachron will offer an ever expanding range of sizes, colours and materials.
Starting in November 2018, Omachron plans to make extrusion equipment available which is 90% smaller and uses 90% less energy than conventional extrusion equipment.
Starting in June 2019, Omachron plans to offer custom molding services for large parts with walls up to 6 inches thick and part weights from a few to a few hundred pounds. Their tooling costs will be low and the resulting parts will have minimal internal stresses, and will therefore not significantly creep, distort or deform when machined or used in applications where the temperature is cycled. Parts as large as 120 inches long, 24 inches wide, and up to 6 inches thick will be possible. Runs from as few as 10 parts per year to several hundred parts per year will be economically viable. Omachron expects that the tooling cost for large parts such as car bumpers will be under $100,000 with a lead time of only six to eight-weeks. It expects that final parts will cost less than $3 per pound plus the cost of the resin chosen.
Starting in June 2020, Omachron intends to start making injection molding equipment available which is 90% smaller and uses 90% less energy than conventional injection molding equipment and uses a new, low-cost, rapid-tooling process.
The Omachron team has also been able to make new LED lighting systems which use 90% less energy than current LEDs. In addition, it has been successful in significantly reducing the size, cost and energy use of equipment for plastic blow molding, plastic rotational molding, metal stamping, metal casting, ceramics manufacturing and glass manufacturing. The company has not yet announced its plans to commercialize these technologies.
Leading Durham Region Engineering Firm excels in Key Sectors
- Air Purification
- Clean Coal and Clean Biomass Combustion Systems
- Compact, low energy use low cost manufacturing and recycling systems for plastics, metals, ceramics and glass
- Energy Efficient Appliances
- Floor Care Products including Vacuum Cleaners
- Efficient Furnaces and AC Systems
- Hydrogen Generation and Storage
- Low Energy LED Lighting and Signs
- Plasma Waste Disposal
- Solar Heating and Air Conditioning Systems
- Sustainable Agriculture
- Water and Wastewater Treatment and desalination Systems