Some of the finest companies have started here, remain headquartered here & are creating products and innovations for the world.
The fourth industrial revolution is under way, and Windsor and Essex County is leading the charge.
With more than 300 companies involved in the engineering, designing and production of cutting-edge manufacturing systems across several sectors, the automotive capital of Canada has become an international hub for automation and emerging technologies. Companies like Brave Control Solutions, CenterLine (Windsor) Ltd., Dieffenbacher North America, Radix Inc., Reko International Group and Valiant TMS are pioneering technologies that are ushering manufacturers across the globe into the digital age.
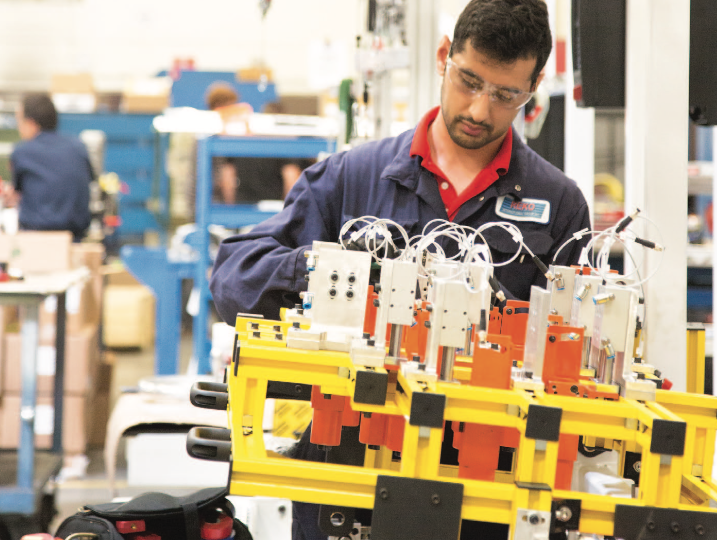
“Part of our role is to be a disruptor,” said Shelley Fellows, vice-president of operations at Radix, which specializes in combining machine vision, advanced robotics and controls, assembly automation and custom software.“Our customers typically are early adopters of technology. So, it’s our job to understand any new technology that’s bubbling up that will disrupt their industry.”
Two years ago, Radix installed the first collaborative robot or “cobot” for the powertrain division of one of the Detroit Three automakers. Cobots, which can perform repetitive tasks, can work alongside humans in a safe manner, and will transform the nature of work, said Fellows.
“Robots with vision systems can adapt themselves to different tasks, and will do more of the work that’s repetitive or dangerous,” she said. “That means workers are going to get accustomed to working with a robot, but they’re also going to focus on tasks requiring intelligence and cognitive ability.”
At Brave Control, president Brent McPhail is positioning his company to become a leader in sensor-based technology that enables manufacturers to acquire and analyze data from every human and mechanized facet of their operation.
“The big term you hear today is Industry 4.0,” said McPhail, whose company uses video game software to build digital twins of machines for the auto industry. “It’s kind of funny because we’ve been doing some of these things since 1996. All we’re talking about is the digitalization of our systems.”
The gathering and analysis of data will help transform today’s plant into the factory of the future, he said.“Imagine everything in the plant, every person, every movement of the individual, every piece of a machinery were being measured.What kind of efficiencies could you unlock?”
“We do a good job of analyzing simplistic, logical sequential systems,” he added.“So the next evolution is analyzing complex systems.”
Automation that sharpens a manufacturer’s competitive edge has been at the core of Reko’s 40-year history, said CEO Diane Reko.
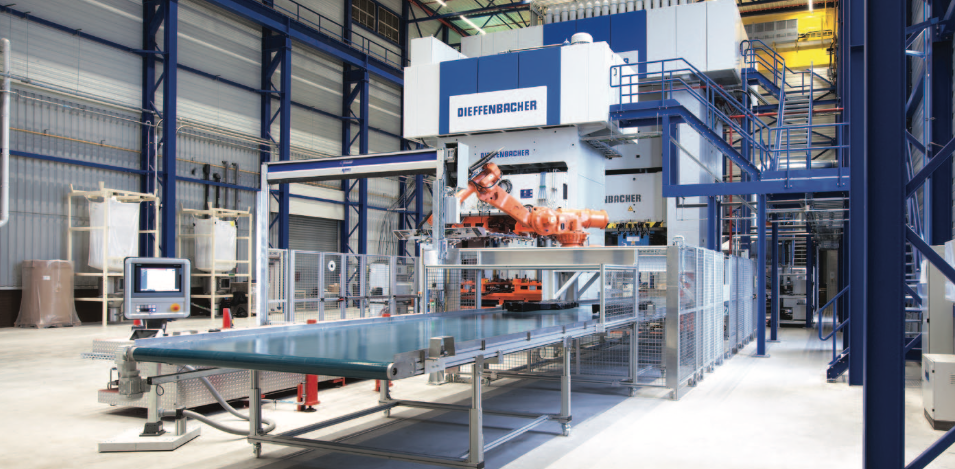
“When we take on a project we’re doing research and development to become better whether it’s machining, producing a tool or designing automation equipment for our customers.” Sensors and the connectivity of the Internet are enhancing the company’s ability to provide remote operational maintenance of customers’ machines, said Reko.
“Sensors built into some of our automation equipment will send a message to our quality guy, telling him ‘this piece of machinery needs to be adjusted just slightly.’And we’re talking about less than a centimetre in one direction or the other.”Trouble-shooting can be done “remotely so the product comes out perfect every time,” said Reko. “You don’t have to stop the machine or check every part. That’s all been automated into the controls and processing.”
The Lakeshore company recently opened a new $5.5 million, 40,000-square foot manufacturing and innovation facility, boosting its footprint to 125,000 square feet.
CenterLine (Windsor) has been setting industry standards since the company was established 61 years ago, said Phil Campbell, vice- president of sales.
“We have 81 patents with more pending, and every year we raise the bar,” said Campbell. “Many of our innovations are even adopted by our competitors.”
The company designs and builds metal-joining and forming products, manufactures automated machinery and welding equipment for the automotive, mass transit, aerospace and defence industries. It employs a full-time department of researchers and product developers whose sole focus is innovation, said Campbell. Tighter fuel economy standards as well as the advent of electric and autonomous cars are influencing changes in materials science and the composition of vehicles, he said. “We’ve made sure we understand changes in materials science and kept up or are ahead of them.We’re always thinking about the next step.”
With more than 1,000 employees, CenterLine has grown from a two-man tool and die shop in 1957 into an international company, generating sales in Mexico, Brazil, China, India and Germany.
“The courage to innovate,” is among the attributes that have made the Dieffenbacher Group one of the world’s leading manufacturers of hydraulic presses and complete plants for the wood and composite industries,” said Louis Kaptur, Research and Development Engineer at Dieffenbacher North America.
The Windsor operation, a subsidiary of the German parent, is ideally located in the region’s growing high-tech cluster, Kaptur said, adding that key benefits include the “large talent pool for employees, and close proximity to the U.S. and southwestern Ontario technology corridor.”
The high density of companies offering automation and advanced technologies for automotive, aerospace, infrastructure, and other sectors “breeds future success through collaboration and healthy competition,” Kaptur said. Ongoing technical developments are opening up new opportunities, he said. “Data acquisition in our systems,
constantly provides feedback to the user from part to part to ensure quality and troubleshoot production challenges.
“As our society moves to Industry 4.0, we will move with it.”
Although in its infancy, Industry 4.0 is already being embraced by Valiant TMS, a 59-year-old Windsor company which has expanded its global presence under new ownership by a Chinese consortium, said Suresh Rama, Director of Engineering and Innovation.
“The world is getting connected; the advent of Industrial Internet of Things (IIoT) is an important event that industry has to get used to and adapt quickly as we march into Industry 4.0,” said Rama.“At Valiant TMS we are not only educators of these technological advances, but we also showcase the value they bring for operational excellence and productivity enhancement for our customers and ourselves.”Valiant TMS’s Windsor operations are playing a leading role in implementing Industry 4.0, he added. “From our Automotive Powertrain Center of Excellence in Windsor, we have designed and built Industry 4.0 ready, material handling systems, and
delivered easy-to-teach collaborative robots to our customers,” he said.“In our Hemming division, we delivered a high speed robotic hemming station capable of 105 jobs per hour with multiple robots working together.”
“We are working closely with our customers to enable virtualization, simulation, collaborative robots, Industrial Internet of Things, artificial intelligence, machine learning, all resulting in the factory of the future, which is self-diagnosing, self-maintaining and always available,” said Rama.
In 2017, the automation and tooling supplier was purchased by Shanghai- based HCD Group, a move that provides “many opportunities to expand our current operations here by opening new markets in automotive and aerospace, which is growing fast in China,” said Rama. Even before the Chinese purchase, Valiant TMS had a formidable global footprint with 27 facilities in 15 countries and more than 1,400 employees.
“The next industrial revolution is a big challenge for the industry as a whole, but we are more than ready here in Windsor-Essex,” said Rama.
If you require more information about this story or the Windsor-Essex Region, please connect with one of the business professionals at Windsor-Essex Economic Development Department who will assist you with location and investment decisions – please email info@choosewindsoressex.com or visit Choose Windsor Essex